Regulations
Each region has its own regulations for air emission control.
In Europe, the legal framework is given by the Industrial Emission Directive 2010/75 EU and the Air Emission Limits related to the Best Available technologies.
In the USA, The overarching air regulation is under the Clean Air Act that establishes 187 hazardous air pollutants to be regulated. “Criteria” air pollutants are those pollutants for which the Clean Air Act directs the U.S. Environmental Protection Agency (EPA) to establish air quality criteria in the form of the National Ambient Air Quality Standards (NAAQS). National Emission Standards for Hazardous Air Pollutants (NESHAP) have been established for industries emitting listed pollutants and generally require the use of Maximum Achievable Control Technology (MACT).
The bottom line is that each source of pollutants, such as an industrial plant, is issued an air permit which spells out exactly what that plant needs to report and limits it has to comply with for each pollutant. The permit also sets the reporting method and the sensing that has to be in place.
Targeted Pollutants
Where to find Hydrochloric Acid (HCl)?
Hydrochloric acid is the main acid pollutant in Waste to Energy (WtE) facilities, but it can also be generated by industrial manufacturing processes such as cement production and some fossil fuel-fired power plants.
Legislations for Hydrochloric Acid (HCl)
There are both national and local laws and regulations regarding HCl emissions. As an example, the new legal framework for Waste to Energy in Europe (BREF WI), requires emission limit values between 2 and 8 mg/Nm³. Thus, HCl has to be removed down to very low values, with removal efficiencies of over 99.9%.
SOLVAir® solution for Hydrochloric Acid (HCl) removal
SOLVAir® ’s sodium-based products, sodium bicarbonate and trona, are very reactive with HCl and allow its mitigation to a very low level (below 5 mg/Nm3) with a high sorbent efficiency.
SOLVAir®, the most efficient sorbents
Dry Sorbent Injection (DSI) of SOLVAir® sodium-based sorbents, upstream of a particulate removal device, is a very simple and efficient process compared to other competing flue gas treatment systems. It enables the removal of HCl at higher rates than other types of dry sorbents.
In addition, the DSI process is totally dry, therefore there is no generation of aqueous effluents needing to be treated.
Neutralization reactions of HCl with SOLVAir® sorbent
Acid neutralization reactions using SOLVAir® sodium-based sorbent:
- ALCALI + ACID GAS → SALT
- NaHCO3 + HCl → NaCl + CO2 + H2O
Acid neutralization reactions using trona:
- NaHCO3*Na2CO3*2H2O + 3HCl → 3NaCl + 2CO2 + 4H2O
SOLVAir® sodium based products are safe, non-corrosive and highly efficient for air emission control!
Where Sulfur Dioxide (SO2) is found
Sulfur dioxide is produced by heat and power generation facilities such as industrial boilers and power plants, but also by the cement, glass, glass fiber, stone wool, ceramics, metal and Waste to Energy industries. The sulfur in the fuel or in the raw material is mainly converted into sulfur dioxide (SO2) during combustion. Typically, over 98% of sulfur oxides in boiler flue gases is SO2, with the remainder being SO3.
Legislation for Sulfur Dioxide (SO2)
There are national and local laws and regulations regarding SOx emissions, as well as industry-level regulations that apply to many different industries such as fossil fuel power generation, combustion plants (LCP), iron & steel (IS), cement and lime, glass, etc. In Europe, these BREFs require emission limit values down to 30 mg/Nm³, and SO2 mitigation rates between 50 and 98%.
SOLVAir® solution to eliminate Sulfur Dioxide (SO2)
SOLVAir® Solution consists in using a Dry Sorbent Injection (DSI) of sodium bicarbonate and trona-based products for cleaning flue gases.
SOLVAir® unparalleled mitigation rates
For some boilers in the utilities sector, treating SO2 with wet scrubbers is too expensive. Dry Sorbent Injection tends to be the most economical choice for these industries. The ground sodium-based product is injected dry and dispersed throughout the duct, allowing SO2 mitigation to very low levels (reductions over 99% have been measured) in order to comply with even the most severe regulations. It is especially effective when there are volatile levels of SO2 to treat.
Neutralization reactions of Sulfur Dioxide (SO2) with SOLVAir® sorbent
Acid neutralization reactions using SOLVAir® sorbent:
- ALCALI + ACID GAS → SALT
- 2 NaHCO3 + SO2 +1/2 O2 → Na2SO4 + 2 CO2 + H2O
Acid neutralization reactions using trona:
- 2 NaHCO3*Na2CO3*2H2O+3SO2+1/2O2 → 3Na2SO4+ 4 CO2+3H2O
SOLVAIR® sodium-based products are safe, non-corrosive and a highly performing solution for air emission control!
Where Sulfur Trioxide (SO3) is found
Sulfur trioxide is produced by heat and power generation facilities such as industrial boilers and power plants, but also in the cement, glass, glass fiber, stone wool, ceramics, metal and Waste to Energy industries. Sulfur present in the fuel or in the raw materials is converted into mainly sulfur dioxide (SO2) during combustion. Typically around 2% of sulfur oxides in boiler flue gases are SO3, with the remainder being SO2. In manufacturing processes, such as ceramics and glass production, this percentage can be much higher.
Corrosion and salt formation issues
As SO3 has an acid dew point above 100°C (212°F), condensation on cold spots can easily occur, generating corrosion on metal parts. Moreover, due to its high reactivity with ammonia (NH3), which forms ammonium salt deposits, very low SO3 levels (less than 10 mg/Nm³) are required in Waste to Energy applications to be able to operate tail-end catalytic DeNOx systems at low temperatures (180-200°C, 356-392°F).
SOLVAir® solution for SO3
The SOLVAir® Solution consists in the Dry Sorbent Injection (DSI) of sodium bicarbonate and trona-based products for cleaning flue gases.
Targeted removal of SO3
By using these products, SO3 can either be specifically removed from a gas stream containing both SO2 and SO3, or reduced to very low levels (< 0,1 mg/Nm³). In some cases, a high removal of SO2 is also targeted concurrently.
Therefore, for industrial processes generating SO3, Dry Sorbent Injection with ground sodium based products is often the most efficient and economical choice.
Neutralization reactions of SO3 with SOLVAir® sorbent
Acid neutralization reactions using sodium bicarbonate:
- ALCALI + ACID GAS → SALT
- 2 NaHCO3 + SO3 → Na2SO4 + 2 CO2 + H2O
Acid neutralization reactions using trona:
- 2 NaHCO3*Na2CO3*2H2O+3SO3 → 3Na2SO4 + 4CO2 + 3H2O
SOLVAir® sodium based products are safe, non-corrosive and a highly performing solution for air emission control!
Fluorhydric Acid is a strong acid, which contributes to acid rain and can heavily impact the flora around an emission point, as well as human health.
Where Fluorhydric Acid (HF) is found
In the production of tiles, expanded clay and bricks, where large numbers of small production units need simple and effective air emission control systems, the SOLVAir® product range enables users to comply with local regulations and cut flue gas treatment costs.
A series of acid gases to mitigate
In tile manufacturing (terracotta tiles, bricks and floor tiles) combustion gas purification systems need to take into account all the main acid pollutants: sulfur dioxide (SO2), hydrochloric acid (HCl) and hydrofluoric acid (HF). The production of enamel and special glass are also concerned by HF emissions.
Legislation for Fluorhudric Acid (HF)
There are national and local laws, as well as industry-level regulations regarding HF emissions. In Europe, for various industries Emission Limit Values for HF are typically 1 mg/Nm³ or lower.
SOLVAir® solution for Fluorhydric Acid (HF)
The SOLVAir® Solution consists in the Dry Sorbent Injection (DSI) of sodium-based products for cleaning flue gases.
Neutralization reactions of Fluorhydric Acid (HF) with SOLVAir® sorbent
Acid neutralization using sodium bicarbonate:
- ALCALI + ACID GAS → SALT
- NaHCO3 + HF → NaF + CO2 + H2O
Acid neutralization using trona: [TM3]
- NaHCO3*Na2CO3*2H2O + 3HF → 3NaF+2CO2+4H2O
SOLVAir® sodium based products are safe, non-corrosive and a highly performing solution for air emission control! With SOLVAir® sodium-based products, local regulations for acid pollutants are easily complied with. Experience has also shown bicarbonate to yield demonstrably effective results.
Particulate Matter (PM) designates fine particles, and aerosols liquid droplets small enough to become airborne. Fine particulate matter (PM10, PM2,5) and acid droplets like SO3 aerosols can penetrate the lungs and greatly impact health.
Where Particulate Matter (PM) and Aerosols are found
Combustion processes using solid or liquid fuels, and various manufacturing processes.
Legislation for Particulate Matter (PM) and Aerosols
There are national and local laws and regulations regarding particulate matter. Particulate matter Emission Limit Values are compatible with the levels that can be achieved by filtration with bag filters, namely 5 to 10 mg/Nm³.
Inhalable limitations
As an example, the European Commission regulates the inhalable fraction of PM pollution (Directive 2008/50/EC on ambient air quality and cleaner air for Europe) because of its ability to enter the lungs and its potential to greatly impact health. There are however no specific Emission Limit Values on fine particulate matter (PM10, PM2,5) yet.
SOLVAir® solution for Particulate Matter (PM) and Aerosols
By using SOLVAir® sodium based products, acid droplets are easily neutralized, and filtration with a bag filter reduces particulate emissions to levels close to zero.
Complementing Electrostatic Precipitators
In some locations, Electrostatic Precipitators (ESP) are the pollution control technology of choice to reduce particulate matter emissions. The use of sodium sorbents injected before the ESP improves its performance, thereby further reducing PM emissions.
Complementing bag filters
When used as a dry sorbent injected into an exhaust duct before a bag filter, sodium bicarbonate will react with acid gases. Our solution, in combination with high performance filtering devices, enables the reaching of PM emissions under 1 mg/Nm3.
Nitrogen oxides are among the most commonly found pollutants. They contribute to the formation of acid rain and are the primary cause of the presence of ground level ozone. They also contribute to particulate formation, and their geographical impact can be extensive as they are easily displaced by winds.
Where Nitrogen Oxides are found
All combustion and manufacturing processes. NOx are generated by any high temperature combustion process where both oxygen and nitrogen are present.
Natural endothermic reactions
These nitrogen oxides are formed as heat from the combustion causes endothermic reactions between nitrogen and oxygen. Nitrogen monoxide (NO) is generally the main component, accounting for 90% of NOx.
Natural gas-fired combustion processes generate NOx as the nitrogen in the air reacts with oxygen. Coal and oil-fired combustion processes, as well as waste and biomass combustion also generate NOx as a result of the oxidation of the nitrogen contained in the fuel.
Legislation for Nitrogen Oxides
For European Waste to Energy facilities, the Emission Limit Value range for NOx is 50 to 150 mg/Nm³. In urban areas, due to the cumulative effect of NOx from vehicle traffic, lower ELVs are often imposed.
SOLVAir® solution for Nitrogen Oxides
The SOLVAir® Solution consists in the Dry Sorbent Injection (DSI) of sodium-based products for cleaning flue gases, which avoids the reheating of flue gases when tail-end catalytic DeNOx systems are used.
A conjunction with SO2 mitigation
When used as a dry sorbent injected upstream of a filter, sodium-based products readily react with acid gases. In some cases, 10-20% of NOx mitigation occurs in conjunction with the removal of SO2.
Limiting ammonium sulfate deposits
NOx reduction is often conducted by installing a Selective Catalytic Reduction (SCR) system, which uses ammonia and a catalyst to convert NOx into N2. The SCR needs to operate at quite high temperatures in order to avoid the deposition on the catalyst layer of ammonium (bi)sulfate. But as sodium bicarbonate has the highest reactivity toward SO2, it leaves a very low level of remaining pollutant, thus minimizing the risk of formation and deposit of ammonium (bi)sulfate.
Increased energy efficiency
Furthermore, the extended operating temperature range of bicarbonate-based sorbents enables to avoid the cooling of the flue gases which is required for other treatment options.
The sum of these facts allows the use of the catalytic DeNOx device at the same temperature as the bag filter, saving the energy needed to reheat the gases and avoiding related CO2 emission. Additionally, another step of energy recovery of the heat from the clean gases can be installed. Finally, SOLVAir® bicarbonate based products are also compatible with non-catalytic DeNOx systems (SNCR), which inject ammonia or urea solutions in the combustion zone.
Where Micropollutants are found
Micropollutants such as dioxins, furans and other Polycyclic Aromatic Hydrocarbons (PAHs), as well as Persistent Organic Compounds (POPs) and other organic carbon compounds are often produced during combustion.
A series of toxic elements
These products are in most cases toxic or harmful for the health of human or animal life and can contaminate agricultural products. Controlling their emission is a fundamental step to avoid their absorption by living organisms.
Legislation for Micropollutants
For European Waste to Energy facilities, the Emission Limit Values are as follows:
- Dioxins & Furans: 0,1ng TE/Nm³
- Organic Carbon compounds (TOC): 10 mg/Nm³
In the USA, there are special provisions to keep track of dioxins and furans but the actual limits are set individually for each permit issued by the authorities. The reporting and enforcement limits are cumulative and as is 0.1 grams for dioxins and dioxin-like compounds and is regulated under Toxic Release Inventory and Section 313 of the Emergency Planning and Community Right-to-know Act (EPCRA).
SOLVAir® solution for Micropollutants
The SOLVAir® Solution consists in the Dry Sorbent Injection (DSI) of sodium-based products for cleaning flue gases.
Effective sorbents complemented with activated carbon
Ground sodium bicarbonate-based products are effective sorbents. In order to meet the most stringent dioxins and furans emissions limits in waste incineration (typically 0.1 ng TE/Nm³), the only thing required is to inject activated carbon (or lignite coke) together with sodium bicarbonate.
An easy system to install
This adsorbent is then separated from the flue gas in the bag filter, which also captures Residual Sodium Chemicals (RSCs).The observed emissions values can be much lower than the limits mentioned above. The only necessary equipment for removing dioxins is a system for storing, dosing and injecting the adsorbent.
Removing multiple pollutants simultaneously
By doing so, other micropollutants (PAHs, POPs, organic carbon compounds, etc.) will also be removed. Additionally, micropollutants will be destroyed by a tail end catalyst device used for NOx control, specifically dioxins and furans.
The most critical heavy metals from an environmental point of view are
Mercury (Hg), Cadmium (Cd), Thallium (Tl), Lead (Pb), Zinc (Zn) and Arsenicum (As).
Where Heavy Metals are found
Heavy metals are toxic and persistent pollutants that are generated in fossil fuel-fired power plants, waste combustion and industrial processes. They are released by the combustion processes either as particulate matter or in a gaseous form. They can accumulate in the food chain and therefore in human and animal tissues.
Legislation for Heavy Metals
The Emission Limit Values (ELV) for Waste to Energy in Europe are as follows:
- Mercury (Hg): < 0.05 mg/Nm3, dry, 11% O2
- Cadmium + Thallium (Cd + Tl): < 0.05 mg/Nm3, dry, 11% O2
- Other heavy metals (total): < 0.5 mg/Nm3, dry, 11% O2
In the USA, under Toxic Release Inventory and Section 313 of the Emergency Planning and Community Right-to-know Act (EPCRA). Mercury compounds reportable limit is 10 pounds, polyaromatic compounds is 100 pounds
SOLVAir® solution for Heavy Metals
The SOLVAir® Solution consists in the Dry Sorbent Injection (DSI) of sodium-based products for cleaning flue gases.
Adding an adsorbent
Heavy metals are easily controlled by adding to the sodium bicarbonate-based product an adsorbent like activated coal or lignite coke.
After the thermal decomposition, the bicarbonate-based sorbent becomes porous and has a high specific surface area (~10 m2/g BET). This enables to remove 20-70% of mercury when used alone, and when used in combination with activated carbon (or lignite coke) on a bag filter, mercury removal rates of over 99% can be achieved.
Compliance with the most stringent limitations
Activated carbon and lignite coke enable compliance with mitigation levels required by the most stringent European Waste to Energy emission limits, for flue gas temperatures below 220°C (430°F). At higher temperatures, mercury removal becomes less efficient. As other heavy metals are less volatile than mercury, the efficiency of their removal is even better.
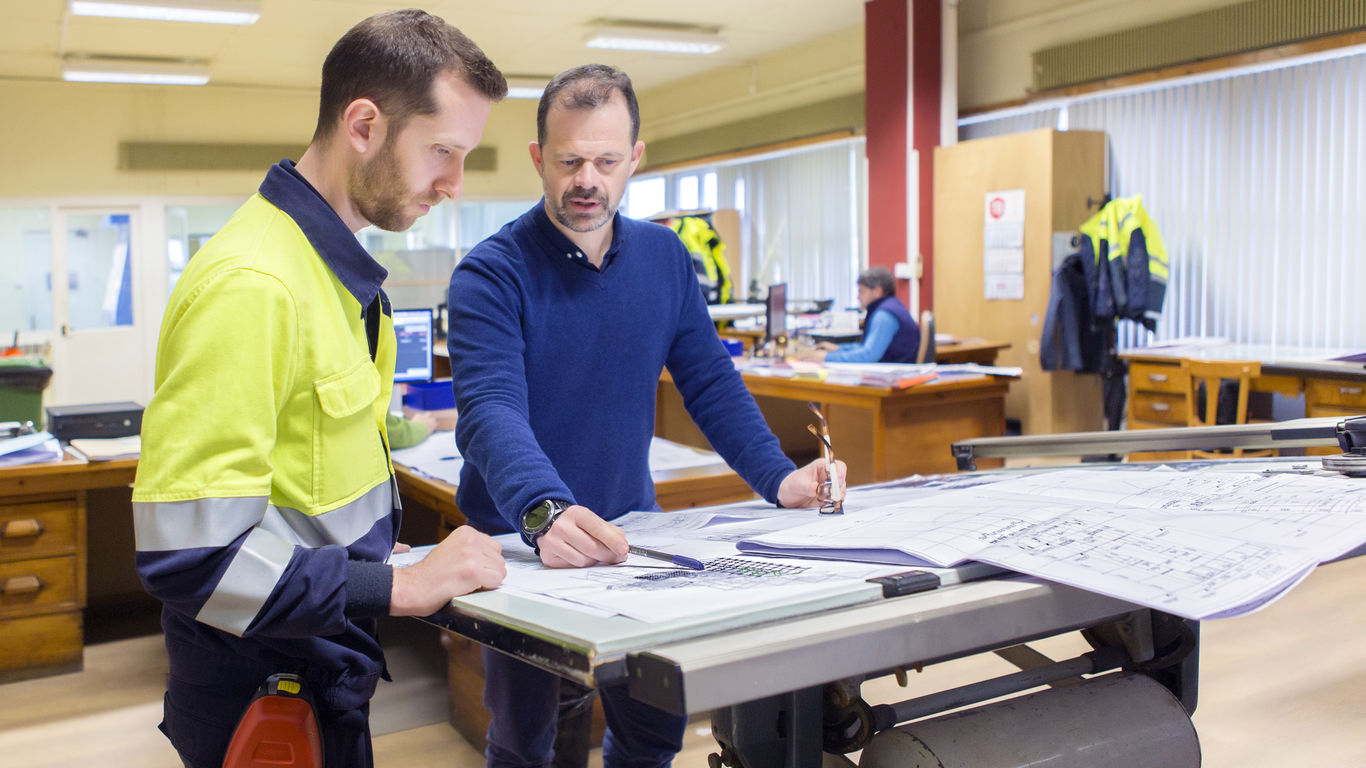
Case studies
See our case studies to get some data!
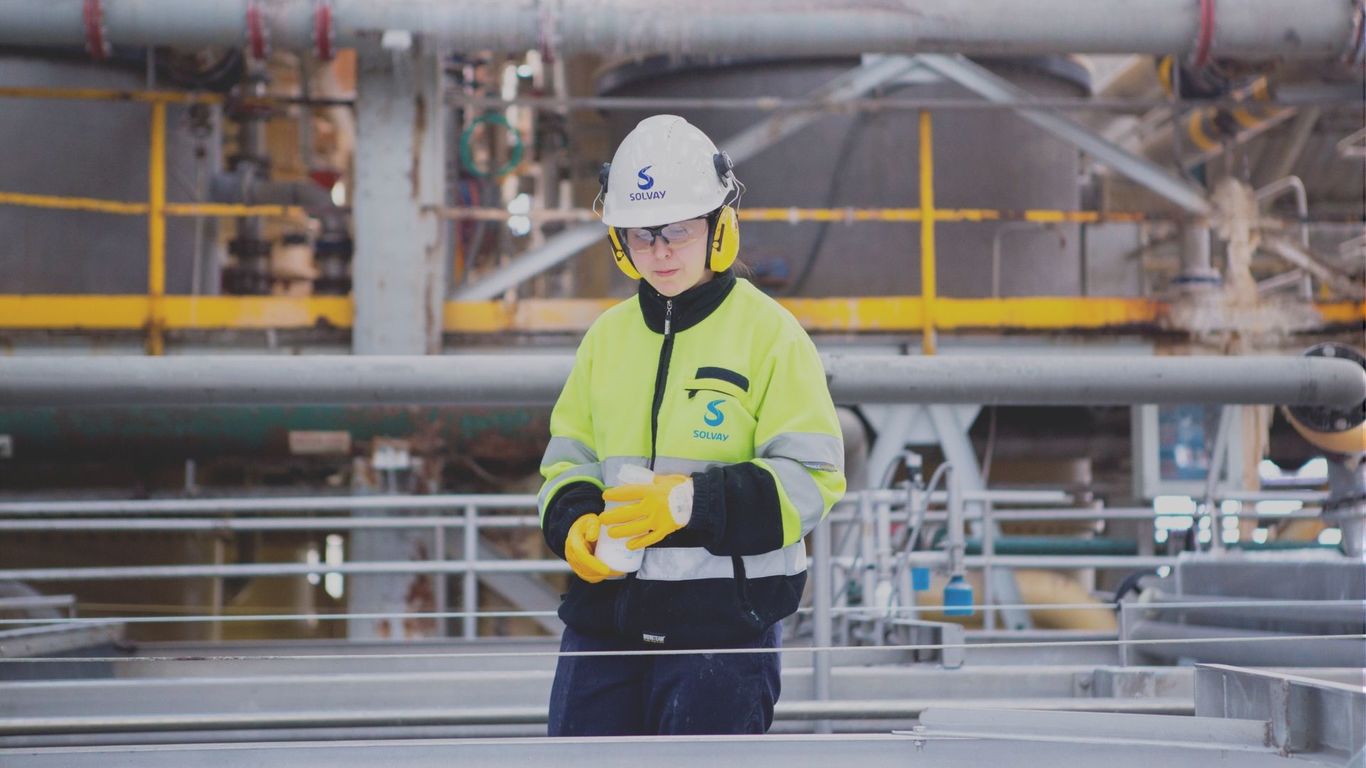
Contact
Any question? Contact our team!