Glass industry and SOLVAir® - Key facts and figures
SOLVAir®is used by major glass manufacturers globally
Flow rate: 35 000 to 75 000 m3/h
Compatible fuels: natural gas and heavy oils
ESP inlet: 300°-400°C
SO2 inlet: 500 – 1700 mg/Nm3 @8%O2 (higher level of SO2 depends on the type of fuel and the type of glass)
SO3 inlet: up to 12% depending on the type of glass
SOx mitigation rate on ESP: up to 98%
Glass industry challenges: Fumes with high sulfur content
There are three main types of glass: flat, container and special glass. All are produced by melting a mixture of sand, sodium carbonate and additives such as sodium sulfate.
This generates dust and acid emissions, mainly sulfur dioxide (SO2) and sulfur trioxide (SO3), coming both from the sulfur contained in the fuel and from the decomposition of the refining agents in the melting furnace.
The challenge of SO3 removal
Typical SO3 contents in flue gases are 7% to 12% in flat glass manufacturing (with natural gas), and 12% - with peaks up to 30% - in container glass, depending on its formulation. Capturing such high amounts of SO3 at high temperatures of 250°C to 400°C is a challenge for glass manufacturers.
Emission limits set by EU regulation
Furthermore, the European Union’s BREF document for Glass Manufacturing sets emissions limits for container glass and flat glass and imposes the use of waste heat for energy recovery, where technically and economically viable.
What SOLVAir® can do for the glass industry
SOLVAir®’s sodium bicarbonate sorbents neutralize the acid components in flue gases to easily comply with legal emission limits. It is highly effective in SOX mitigation as well as hydrofluoric acid (HF), reaching removal rates of 98% of SOx.
The salts formed by these reactions have to be separated from the flue gas using an electrostatic precipitator (ESP) or a ceramic filter, depending on the required mitigation performance and the temperature of the gases.
Providing a competitive advantage to glass manufacturers
SOLVAir® allows heat recovery from the flue gases. This process requires low concentrations of SOx and particularly SO3 in the gases entering the heat recovery system to avoid the condensation of acids inside flue gas ducts, filtration systems and heat exchangers.
High efficiency towards SOx enables glass manufacturers to achieve substantial savings of energy, which can be a decisive advantage in a very competitive industry.
Key benefits for our customers in the glass industry
SOLVAir® is used in a dry sorbent injection system (DSI), which is easy to implement, doesn’t produce any liquid residue and doesn’t require reheating the flue gases to operate a DeNOx SCR.
SOLVAIR® solutions also offer a wide range of operational temperatures, with no observed differences in efficiency in the glass industry.
Recycling the residue into raw material
Furthermore, when using sodium bicarbonate for capturing SO2 and SO3, the residual sodium chemicals consist essentially in sodium sulfate and sodium carbonate, which can be reused as raw material for glass production, thus saving resources and eliminating waste.
Better for SCR operation
Finally, SOLVAir® facilitates the safe operation of a DeNOx SCR, as lower SO3 contents in the gases that enter the SCR improve its operation by avoiding the formation of alkali salts. Customers are also able to operate their SCR at lower temperatures.
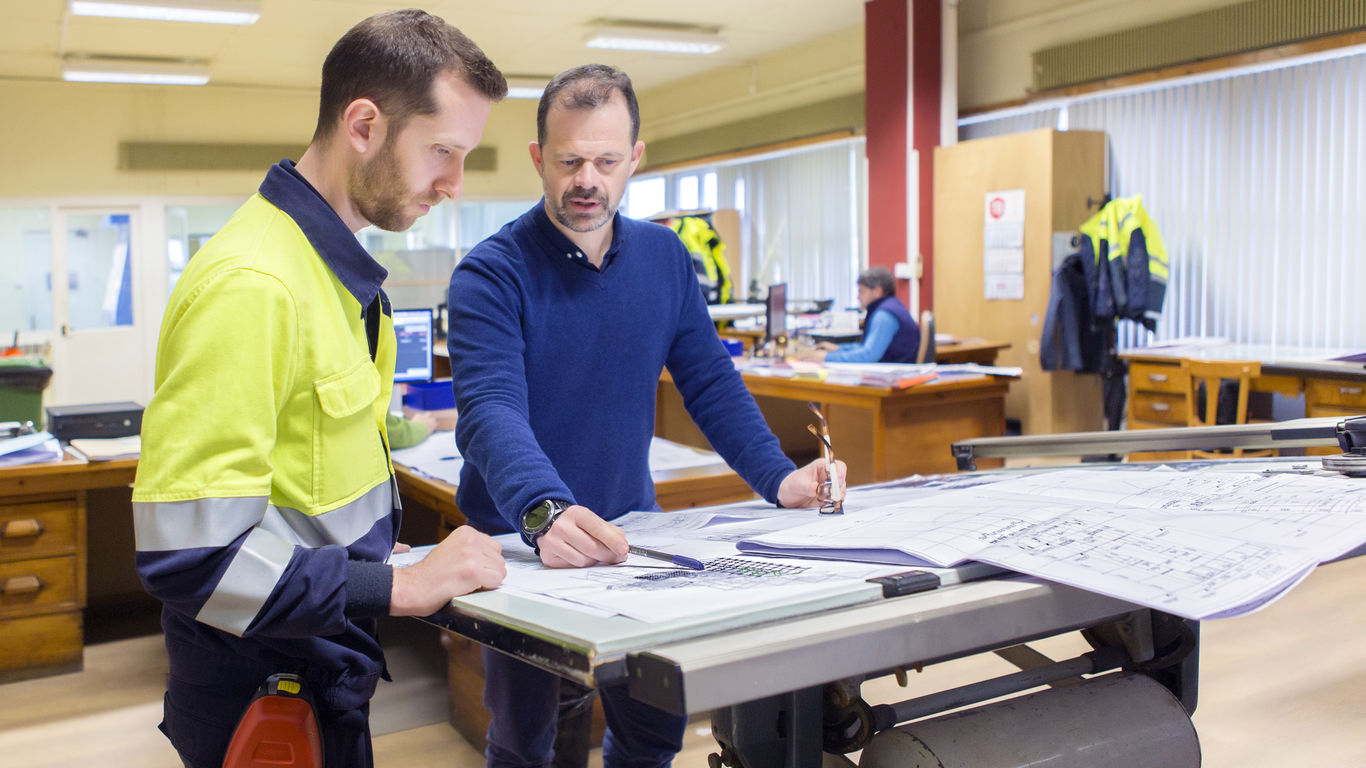
Case studies
See our case studies to get some data!
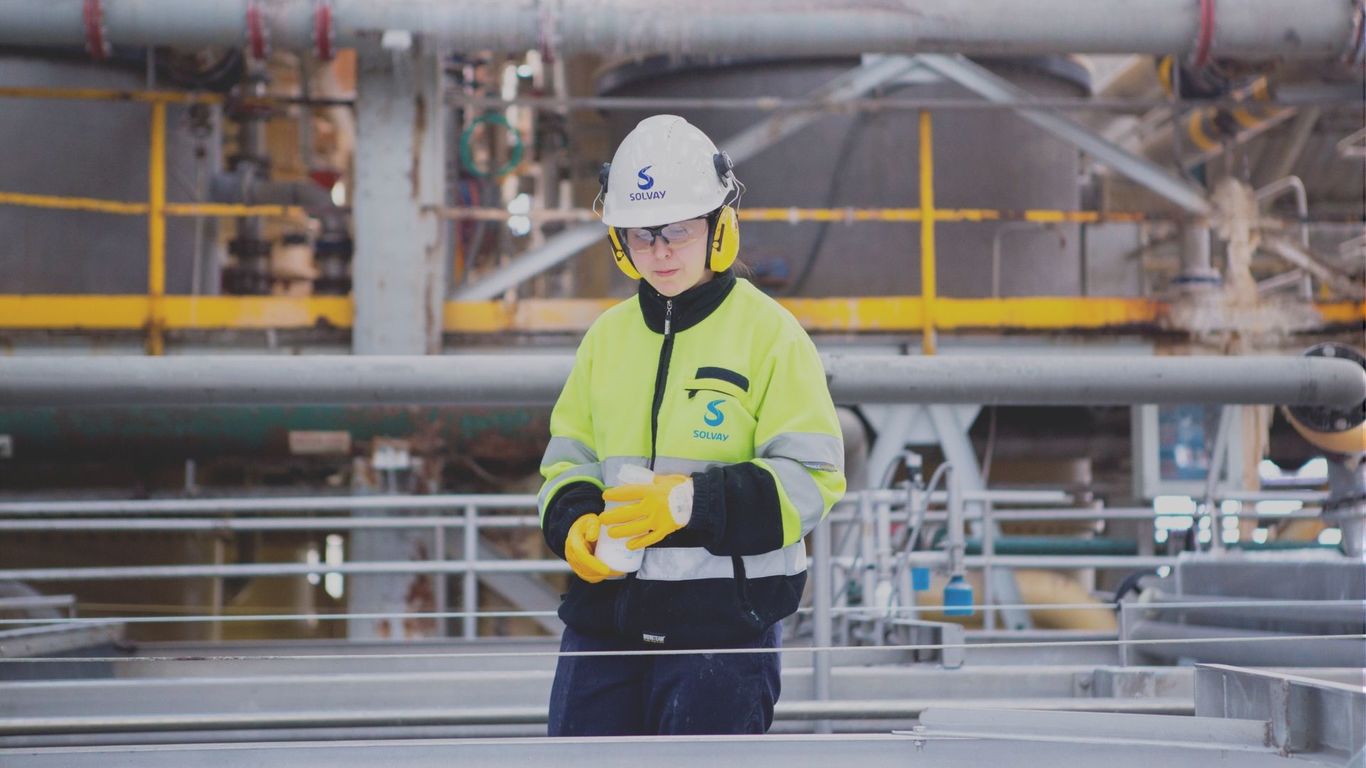
Contact
A question? Contact our team!